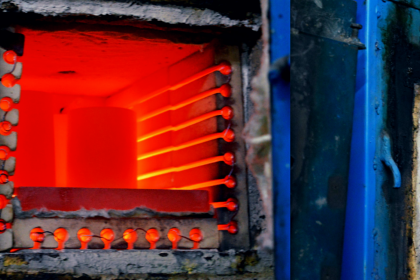
The ceramic tree is then baked (stoked) at high temperatures and reaches its final strength through the sintering process. Any wax remains are burned out during this process.
Before burning the investment is allowed to completely dry, which can take 16 to 48 hours. Drying can be enhanced by applying a vacuum or minimizing the environmental humidity. It is then turned upside-down and placed in a furnace or autoclave to melt out and/or vaporize the wax. Most shell failures occur at this point because the waxes used have a thermal expansion coefficient that is much greater than the investment material surrounding it, so as the wax is heated it expands and induces great stresses. In order to minimize these stresses the wax is heated as rapidly as possible so that the surface of the wax can melt into the surface of the investment or run out of the mold, which makes room for the rest of the wax to expand. In certain situations holes may be drilled into the mold beforehand to help reduce these stresses. Any wax that runs out of the mold is usually recovered and reused.
The mold is then subjected to a burnout, which heats the mold between 870 °C and 1095 °C to remove any moisture and residual wax, and to sinter the mold. Sometimes this heating is also used as the preheat, but other times the mold is allowed to cool so that it can be tested. If any cracks are found they can be repaired with ceramic slurry or special cements.